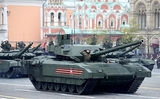
Фото: globallookpress.com
Сам факт того, что после десяти лет «повышенного» внимания правительства к отечественному станкостроению ведущий производитель танков вынужден кривым путем добывать импортные станки говорит о том, что внимание это какое-то кривое.
Чешская компания Gearspect Group a.s. отказалась поставлять комплектующие для станков, которые производит российская корпорация «Уралвагонзавод» (УВЗ), сообщило агентство «Интерфакс». Руководитель управления Федеральной антимонопольной службы (УФАС) по Свердловской области Дмитрий Шалабодов рассказал, что такое решение было принято чешской компанией из-за экономических санкций, наложенных на Россию США и Евросоюзом. «24 июля 2017 года, несмотря на ранее достигнутые договоренности, Gearspect Group a.s. отказалась заключать контракт на поставку оборудования»,— рассказал он.
Зубообрабатывающее оборудование для входящего в УВЗ предприятия «Завод N9» должна была поставить в июне 2017 года пермская компания ООО «Пром-Ойл», которая в свою очередь собиралась приобрести его у чешской компании Gearspect Group a.s., для чего заключила с ней соглашение о гарантированных поставках.
Однако, когда на чешском предприятии узнали, что комплектующие будут перепроданы УВЗ, в поставках было отказано. «Мы не сможем выполнить наш предварительный договор в силу того, что правительство нашей страны нам не рекомендовало проведение процедур поставки по этому контракту»,— говорится в письме Gearspect Group a.s. От участия в договоре банковской гарантии отказалсяРайффайзенбанк.
Утечка информации, в результате которой УВЗ лишился комплектующих для станков, на которых делают танковые орудия, произошла из-за того, что чехи узнали о том, что пермское предприятие участвовало в тендере на их поставку для УВЗ, который находится под санкциями с осени 2014 года. Все эти сведения находились в открытом доступе, и было бы вообще странно и удивительно, если бы чешские бизнесмены поленились зайти на сайт госзакупок и остались в неведении об этой незатейливой хитрости.
Но они не поленились, и теперь на УВЗ будут проблемы с производством современных танковых пушек.
Отметим, что Чехия до 2014 года тесно сотрудничала с уральскими машиностроителями и металлургами, поставляя на Урал станки и оборудование как в советские, так и в постсоветские времена.
В 70-е и 80-е годы на промышленных площадках Уралмаша, Нижнетагильского металлургического комбината (НТМК) и УВЗ монтировалось чешское оборудование для целых технологических цепочек. В конце 90-х, когда чешские станки стали устаревать, руководители машиностроительных предприятий Урала «попросили содействия у ММиВЭС – в восстановлении утраченных связей». Содействие было оказано, посол Чешской республики Любуш Добровский посетил Екатеринбург и подписал соответствующий меморандум с губернатором Свердловской области Эдуардом Росселем, после чего поставки чешских станков и оборудования на Урал возобновились и, как казалось нашим промышленникам, будут продолжаться вечно.
О необходимости импортозамещения никто и не думал. На фоне общего обвала российского станкостроения закупка качественных чешских станков казалась вполне обоснованной. Так началась агония российского станкостроения, нижней точкой которой стал посткризисный 2009 год.
Станкостроение было слабым звеном российской индустрии еще с царских времен. Несмотря на то, что по объемам производства Россия была пятой экономикой мира, ведущие заводы России были укомплектованы образцами станков из стран Западной Европы, в основном из Англии и Германии. Российские промышленники стремились приобретать станки с лучшими эксплуатационными качествами. Когда в первом десятилетии ХХ века военное министерство России решило начать выпуск наиболее передовых для того времени подводных лодок серии «Акула», для Балтийского завода были приобретены новейшие немецкие станки.
До революции ведущие станкостроительные предприятия российской империи были сосредоточены в Санкт-Петербурге и Москве. Многие из них были основана выходцами из Европы. Так, будущий московский завод «Красный Пролетарий» был основан в 1896 г. братьями Бромлеями – обрусевшими выходцами из Англии. В 1868 году англичанин Дж. Мюргед основал в Санкт-Петербурге на Васильевском острове небольшой завод, ставший впоследствии Товариществом машиностроительного завода «Феникс». В 1919 году предприятие было национализировано, получив название «Ленинградское станкостроительное производственное объединение (ЛСПО) им. Я. М. Свердлова».
А вот первенец советского станкостроения московский завод имени Орджоникидзе был построен в годы первой пятилетки, и в 50-е годы стал крупнейшим в мире производителем токарно-карусельных станков.
Индустриализация СССР в годы первых пятилеток была осуществлена, благодаря масштабным закупкам станков и оборудования из Европы и США. Импортные станки стоили дорого, их берегли, и к работе на них допускали только самых подготовленных станочников. В конце 70-х годов министерская комиссия обнаружила на одной из подмосковных текстильных фабрик ткацкий станок английского производства, выпущенный в 1855 году. Станок был в хорошем состоянии и прекрасно работал. Этот случай был высмеян на страницах юмористического журнала «Крокодил», хотя тут впору было всерьез озадачиться Госкомитету по науке и технике. Как бы то ни было, в советское время при наличии мощнейшего станкостроения все сложные технологические операции, как в ВПК, так и на гражданке, производились только на импортном оборудовании.
После Великой Отечественной войны парк станков был существенно пополнен трофеями и репарациями из Германии. Советское станкостроение никогда не выпускало все виды необходимых промышленности станков, да и задачи такой не ставилось. В рамках СЭВ выпуск ряда модификаций станков и оборудования для предприятий всех стран-участниц осуществляли ГДР и Чехословакия. Ряд уникальных станков закупался в Японии. Однако основную часть станков, используемых на предприятиях Советского Союза, составляли станки отечественного производства. Больше всего станков выпускала Российская Федерация, производство металлорежущих станков в РФ составляло около 50 процентов от общесоюзного. Начиная с 70-х годов, оно составляло от 100 до 110 тысяч в год.
В 1990 г. СССР был на втором месте в мире по потреблению металлообрабатывающего оборудования и на третьем месте по его производству. Станочный парк насчитывал свыше 5,5 млн. единиц оборудования, а годовая потребность промышленности составляла около 200 тыс. станков. Отрасль развивалась опережающими темпами (на 1–2 % ежегодно) по отношению ко всей отечественной промышленности. После распада СССР в РФ остались предприятия, производящие лишь 65–70 % от общей номенклатуры продукции станкостроительного комплекса бывшего СССР. За период с 1992 года по 2010 год объем производства металлорежущих станков и кузнечно–прессового оборудования в России сократился в натуральном выражении в 17,8 раза (с 69,9 тыс. шт. в 1992 году до 3,9 тыс. в 2010 году).
Но даже в советское время все сложные технологические операции, как в ВПК, так и на гражданке, производились только на импортном оборудовании. Между тем, за последние тридцать лет в мировом станкостроении произошли целых три революции – геополитическая, технологическая и институциональная. Первая – геополитическая. Китай стал мировым лидером станкостроения. Китайцы «подрубили под корень» российское станкостроение в его наиболее сильном месте – производстве самых простых и дешевых станков, старательно скопировав советское оборудование, и сейчас с ними стало невозможно конкурировать по цене. В 2010 году Китай (годовой объем производства 19 млрд 980 млн. долларов, темп роста 30%) увеличил отрыв от занимающей второе место Японии (объем производства 11 млрд 842 млн и темп роста - 69%). Китай стал и крупнейшим импортером станков. В 2010 году потребление металлообрабатывающего оборудования КНР составило около 46 % от мирового.
Вторая революция – технологическая. Изменились не только сами станки, но и технология их производства и применения. Сегодня автоматизированная станкостроительная цепочка выглядит так: цифровое проектирование детали – программа ЧПУ для ее изготовления на станках – программа ЧПУ для управления роботизированным участком.
Третья революция – институциональная. Современные станкозаводы превратились в сборочные производства. Все стандартизированные модули для будущих станков собираются в узкоспециализированных центрах, откуда затем и поступают на сборочный станкозавод. Лидеры мирового станкостроения переформатировали отрасль таким образом, что производством наукоемких комплектующих занялись «локальные центры компетенций». Так, электрошпиндели выпускает одна компания, револьверные головки - другая, шарико-винтовые передачи - третья, системы ЧПУ разрабатывает четвертая. На последнем этапе станкозавод только собирает станок из готовых деталей.
Организация таких станкостроительных кластеров позволила снизить себестоимость и поднять качество производства. Ключевое звено кластера – системный интегратор, который проектирует и формирует все производственные звенья, а затем обеспечивает запуск и последующее обслуживание производства.
В 1991 году СССР произвел, как я уже писал, около 110 тыс. станков, занимая третье место в мире после США и Германии, по импорту станков страна занимала второе место после США. Сегодня по производству и импорту станков РФ занимает 15-е и 16-е места мире. За последние 25 лет производство металлообрабатывающих станков сократилось более, чем в 20 раз. Наибольший спад производства металлообрабатывающих станков был отмечен уже в новейшие времена — в 2009 г. — на 58,5% относительно предшествующего года.
По приблизительным оценкам, к 2009 году перестали функционировать около 40 станкостроительных предприятий - примерно четверть всех российских производителей. Прекратил своё существование московский станкозавод им. Орджоникидзе. Сейчас на его месте – торгово-развлекательный центр «Гагаринский». В 2003 году было обанкрочено петербургское объединение им. Свердлова, в 2005 году в административном здании был открыт бизнес-центр «Феникс». В 2010 году было прекращено производство на заводе «Красный Пролетарий».
Наибольшее падение произошло в производстве наиболее высокотехнологичных станков. В 2012 г. было произведено всего 4 обрабатывающих центра, внутренний рынок заполонили станки иностранного производства. В результате зависимость российской промышленности от импорта металлообрабатывающих станков выросла в среднем до 80%.
Правительство отреагировало на упадок отрасли в 2007 году, когда Денис Мантуров, в то время замглавы Минпромэнерго (ныне - Минпромторг), предложил создать станкостроительный холдинг, чтобы объединить госактивы в отраслевых предприятиях для создания «точки сборки», после чего в состав холдинга, как предполагалось, радостно и в добровольном порядке вольются частные производители станков.
Рабочая группа Минпромэнерго объявила о намерении создать на базе университета «Станкин» Государственный инжиниринговый центр, по сути головной НИИ отрасли. Этот центр был открыт в 2008 году. А в 2013 году «Ростех» создал «Станкопром»: по замыслу - системный интегратор российской станкостроительной отрасли. Основой развития отрасли должна стать подпрограмма «Развитие отечественного станкостроения и инструментальной промышленности» на 2011−2016 годы в рамках федеральной целевой программы «Национальная технологическая база» на 2007−2011 годы. Она координируется с другой федеральной целевой программой−«Развитие оборонно–промышленного комплекса Российской Федерации на 2011– 2020 годы». Все эти программы призваны помочь в организации большого числа опытно–конструкторских работ по созданию новых образцов станков: новейших видов многокоординатных высокопроизводительных металлорежущих станков с ЧПУ, сверхпрецизионных станков с ЧПУ для механической обработки деталей с точностью до 100 нм и наукоемких комплектующих изделий для узкоспециализированного станкостроения.
В программу включено освоение импортных станкостроительных ноу-хау путем прямой закупки технологий и локализации иностранного производства в России. Анонсировано создание станкостроительных кластеров на Урале, в Ульяновской, Ростовской и Липецкой областях, в Санкт-Петербурге и Татарстане. Крупнейшим станкостроительным кластером РФ на сегодняшний день является холдинг «Стан», сформированный на базе Стерлитамакского станкостроительного завода. В «Стан» вошли производители из Коломны, Рязани, Иваново и Москвы.
Как правило, частные предприятия вынуждены присоединяться к холдингам, участвующим в госпрограммах из-за того, что вне госпрограмм кредиты станкостроителям выдаются под слишком высокий процент.
«Кредиты? Да чего тут говорить. Мы как будто работаем «под банки», словно все специально организовано именно для этого, - говорят в отделе маркетинга Владимирского станкостроительного завода. – «Процент зависит от того, на какой срок берешь кредит. Он бывает больше среднего значения в 16%».
По итогам 2015 года на этом заводе была зафиксирована прибыль всего лишь в 955 тыс. руб. при стоимости активов предприятия в 53 млн руб. Замечу, что обе цифры крайне малы и не отражают реальных возможностей предприятия при разумной кредитно-финансовой политике государства.
На Коломенском заводе тяжелого машиностроения в том же году был убыток в 17 млн. руб., на Симбирском станкостроительном заводе (в стадии конкурсного производства) - убыток в 67 млн. руб., Ульяновский станкостроительный завод - DMG Mori закончил 2015 год с убытком в 166 млн. руб.
Не все российские станкостроительные предприятия убыточны, но ужесточение США и Евросоюзом экономических санкций делает надежды на системное оздоровление и развитие отрасли весьма призрачными.
Сегодня российские станкостроители производят исчезающе малое количество современных станков: в 2016 году было произведено всего 250 автоматизированных станков с ЧПУ.
Нельзя не сказать и о еще одной проблеме, связанной с закупкой иностранных станков и в целом с кооперацией с зарубежными производителями. Станки с ЧПУ подсоединены к GPS и интернету и без этого не работают. Причем, в случае войны производство уже нельзя будет вывести из-под ракетного удара противника, переведя завод в другое место, как это было сделано перед Великой Отечественной, когда предприятия из западной части страны были вывезены на Урал.Производитель оснащает станок GPS-сенсором и гироскопом. В случае перемещения станок автоматически блокируется до получения кода разблокировки от производителя. Даже если станок никуда не перемещается, его всегда в случае можно без проблем отключить дистанционно и полностью парализовать производство даже в другой стране.
На промышленных инженерных форумах пишут:
«Израильтяне русского происхождения давно уже своим российским коллегам в неформальной обстановке говорят прямым текстом, что в случае необходимости США и их союзники заблокируют работу любой западной техники на территории России».
На форуме «Practical Machinist» развернулось, например, обсуждение, как можно разблокировать фрезерный станок с ЧПУ, который отказывается функционировать после перемещения на новое место. Компания купила восемь ЧПУ-фрезеров Mori/Ellison NV5000A, а вскоре перевезла их на другой завод. После этого оборудование вышло из строя. Фирма-производитель объяснила, что таково новое требование американского законодательства и все будущие модели ЧПУ-фрезеров высшего класса будут блокироваться при перемещении на новое место.
Коллеги пострадавшего владельца импортного станка на форуме подтвердили, что аналогичная функция с GPS-блокировкой присутствует и на других ЧПУ-фрезерах высшего класса японского производства, в том числе на фрезерах Citizen. По их данным, что изменения в законодательстве приняли после того, как одного из японских производителей уличили в нелегальном экспорте высокоточного оборудования в Иран и Северную Корею, нарушая эмбарго».
Тем не менее нелегальный ввоз станков в попавшие под запретительные санкции страны и предприятия продолжается. Случай с чешскими станками для УВЗ уже не первый, достаточно вспомнить пресловутые сименсовские турбины для Крымских ТЭЦ.
На прошедшей недавно выставке «Металлообработка 2017» ведущий российский производитель станков холдинг СТАН показал станки, которые, как отметили посетители выставки, в СССР делались в 90-е годы, а в мире – 50 лет назад. Холдинг имеет портфель госзаказов на сумму примерно 1,7-2 млрд. рублей и благодаря этому держится на плаву, хотя его дочерние предприятия находятся не в лучшем состоянии.
«Принудительное размещение заказов, это хоть что-то для реальной помощи, но всё же заказы от ОСК, ОАК и КТРВ (Корпорация «Тактическое ракетное вооружение» – В.П.) это скорее аппарат искусственного дыхания для пациента, который уже 30 лет лежит в коме», - комментирует посещение этой выставки Вячеслав Яковлев, менеджер и акционер «Кубаньжелдормаша».
Яковлев дает пессимистический прогноз: на станкостроение «тратят и будут тратить миллиарды из государственного бюджета под видом «спасения, поддержки, помощи, восстановления» и так далее. И абсолютно всё это уйдет в карманы, ни один завод не вернут к жизни. Если не верите, давайте через пять лет вернёмся к этой теме. Будет много уголовных дел про растраты выделенных средств на НИОКР и строительство, официальные банкротства предприятий, смена ООО на ПАО и ПШИК на выходе. Специалистам ждать не надо, они и так всё знают. Не хочу углубляться в доказательства и тем более споры с теми «управленцами», которые сегодня осваивают на широкую ногу деньги из бюджета.
Если бы не было скандалов со строительством космодрома «Восточный» и докладов Счетной палаты о коррупции в российском ВПК, если бы не было резонансного возрастания стоимости строительства питерской «Зенит-Арены», крышу которой только что до дыр злодейски проклевали бакланы, то можно было бы списать эту жесткую оценку ситуации в российском станкостроении на простую зависть к более успешным конкурентам.
Но сам факт того, что после десяти лет (то есть двух пятилеток!) повышенного внимания правительства к отечественному станкостроению ведущий производитель танков вынужден кривым путем добывать импортные станки, без которых пушки замечательных «Армат» будут криво стрелять, говорит о том, что внимание это, уж извините за тавтологию, какое-то кривое.
Если глава Минэкономразвития берет то ли взятку, то ли премию, то ли миллионом долларов, то ли «колбасой»; если чуть ли не каждый день нам сообщают о задержании функционеров спецслужб, если ЦБ банкротит отечественные банки с подозрительной избирательностью, смахивающей на личный и корпоративный интерес, то с какой стати в российском станкостроении должно быть иначе?
Поэтому, как представляется, скандалы с попытками кривого ввоза импортного оборудования будут множиться и далее. И с той же регулярностью они будут разоблачаться, давая Западу повод к ужесточению и без того жестоких санкций.
Однако, пришло время ответить на вопрос, сформулированный в заголовке:Почему Уралвагонзавод пытался импортировать чешские станки «кривым путем»?
Ответ прост: от безвыходности.
Владимир Прохватилов, президент Академии реальной политики (Realpolitik), эксперт Академии военных наук
Больше новостей и ближе к сути? Заходите на ленту в Телеграм!
Добавляйте CСб в свои источники ЯНДЕКС.НОВОСТИ.
//Партнер Гнездо.ру
Картина дня
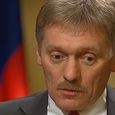
Песков: Кремль намеренно не раскрывает все детали беседы Путина и Трампа по урегулированию
Зампред ВТБ Пьянов уверен в снижении ключевой ставки 12 сентября

Лукашенко заявил картофелеводам, что не хотелось бы управлять страной по-диктаторски, «но пока не получается»

Минпросвещения и Дума рекомендовали петь в школах и детсадах песни Шамана и Газманова

Бывшего директора Театра сатиры задержали по делу о мошенничестве

На Александра Цекало подала в суд его бывшая супруга Виктория Галушка

Прилучный и Брутян о свадьбе Муцениеце: "Красивая дата, счастья молодым!"

//Новости giraff.io
Наши публикации
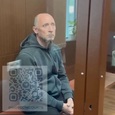
Новости с фронтов борьбы с коррупцией: арест вице-губернатора, задержание мэра, приговор трем генералам
Гендиректор РКК "Энергия" заявил, что предприятие на грани разорения и вытащить его – "задача из области чуда"

"Ъ": полномочия Бастрыкина на посту председателя СКР продлены, полпредом в этом году он не станет

После резонансной трагедии на Пике коммунизма в Думе предложили запретить восхождения без гидов

Хрен да каша пища наша?

Правительство предложит россиянам добровольно ограничивать себе доступ к опасному контенту в интернете

ЦБ перечислил признаки мошеннических операций при снятии наличных в банкоматах

Слухи, скандалы, сплетни
Дмитрий Дибров о разводе: "Сейчас не самые веселые времена в моей жизни"

В Южной Корее исполнителя Gangnam Style проверяют по делу о запрещенных веществах

На Александра Цекало подала в суд его бывшая супруга Виктория Галушка

Прилучный и Брутян о свадьбе Муцениеце: "Красивая дата, счастья молодым!"

Шоубиз
Ксения Бородина вышла замуж за Николая Сердюкова

Виктория Боня о своем восхождении на Эверест: "Удивило молчание коллег по шоу-бизнесу"

Наука
SpaceX успешно запустила Starship после нескольких неудачных пусков

Роскосмос сообщил об устранении утечки воздуха на модуле "Звезда" МКС, о которой известно с 2019 года

«Яндекс» планирует заняться созданием человекоподобных роботов

Корабль Blue Origin с Кэтти Перри и невестой Безоса совершил полет в космос

Хайтек
В сеть утекли 16 млрд паролей от аккаунтов Apple, Google и других сервисов

Разработчики ПО для российской ОС «Аврора» подали заявление о банкротстве

В ФСБ рекомендовали откаться от использования российского браузера "Спутник"

Ъ: В российских кнопочных телефонах обнаружили уязвимость, которая позволяет управлять телефоном посторонним

Туризм
В Европе готовятся запустить новую систему пограничного контроля - контроль за пребыванием ужесточится

Песков: В Кремле не видят новизны в заявлениях Трампа

За поездки за рубеж предложили ввести сбор

Болгария внесла изменения в список документов на получение визы

Спорт
Станислав Черчесов стал главным тренером грозненского «Ахмата»

Дегтяреву неловко называться президентом и он просит себя переименовать

Двукратная олимпийская чемпионка по биатлону Лаура Дальмайер погибла в горах Пакистана

«Оренбург» сыграет вместо исключенного «Торпедо» в новом сезоне РПЛ

МВД назвало размер взятки арбитру за помощь «Торпедо» в решающем матче

«Торпедо» исключили из числа участников РПЛ, но клуб «будет жить»

Вкусный раздел
Юлия Дианова: Не просто завтрак

Дарья Близнюк: «Заготовки от Даши. Вкусно, как ни «крути»!

Анна Аксёнова: Муссовые торты. Легче легкого!

Софи Дюпюи-Голье: Мир хлеба. 100 лучших рецептов домашнего хлеба со всего мира
