
Американский военный эксперт Питер Уоррен Сингер из «New America Foundation» опубликовал на своем сайте статью о перспективах применения 3D принтеров в производстве вооружений и военной техники.
Он считает, что «прямое цифровое производство» (Direct digital manufacturing), иначе называемое 3D принтинг, в самое ближайшее время совершит вторую промышленную революцию в военной промышленности по образу и подобию первой революции, которую, как пишет Сингер, совершил Сэмюэл Кольт, изобретатель знаменитого шестизарядного револьвера «Миротворец».
Кольт переосмыслил производственный процесс, используя взаимозаменяемые детали, и сделал возможным производство оружия в небольших мастерских. Такую же революцию в свое время произвел ткацкий станок.
С помощью 3D-печати уже пробуют выпускать авиационные реактивные двигатели. Из тех 3D печатных новинок, о которых упоминае Сингер, я бы выделил показанные на недавней выставке Sea-Air-Space Expo CICADA (Close-In Autonomous Disposable Aircraft) – крошечные одноразовые самолетики, управляемые дистанционно, то есть дроны. Рой таких дронов, которые крайне дешевы в производстве и проектировании, может наводнить территорию врага и сделать его беззащитным, парализовав системы ПВО.
Сингер упоминает и другой важный аспект применения 3D печати – концентрация полного производства любого изделия в одном месте. Сегодня военное производство рассредоточено по десяткам смежных предриятий, выпускающих комплектующие для ракеты, самолета или автомата. А 3D печать дает возможность производить военную технику на одном предприятии.
Заметим, что на такой метод производства уже перешел знаменитый Илон Маск.
Справка:
И́лон Рив Маск (англ. Elon Reeve Musk; род. 28 июня 197 года в Претории, ЮАР) — канадско-американский инженер, предприниматель, изобретатель и инвестор; миллиардер. Основатель компаний SpaceX и PayPal (последняя была продана в 2002 году за 1,5 млрд долларов, а в 2015 году была оценена в 44 млрд $).
Основатель, владелец, генеральный директор и главный инженер SpaceX; главный дизайнер (Chief Product Architect),генеральный директор и глава совета директоров Tesla Motors. (Википедия)
Границы применения трехмерной печати в промышленности непрерывно расширяются. Переход от лазерного спекания к лазерной плавке приближает прочностные свойства напечатанных изделий к литым.
Ведущие позиции в печати лазерным спеканием и плавкой занимает американская 3D Systems.
Лидер в производстве 3D принтеров методом «электронно-лучевой плавки» (EBM – Electron Beam Melting), так называемого аддитивного производства - шведская компания Arcam.
Технология EBM основана на том же принципе, что и технология лазерной плавки, только вместо лазерных лучей используются электронные лучи высокой мощности.
Минус этого метода – рентгеновское излучение, возникающего при бомбардировке металлов высокоэнергичными электронами («тормозное излучение»), что требует установки поглощающей лучи защиты.
Электронно-лучевая плавка позволяет создавать жаростойкие форсунки и лопатки газовых турбин, включая реактивные двигатели, а также несущие титановые элементы крыльев самолетов.
Аддитивное производство привлекло внимание НАСА. В первую очередь это касается создания элементов ракетных двигателей: камер сгорания и форсунок со стойкостью к температурам свыше 3000°С. Высокое давление и температура требуют использования тугоплавких и прочных материалов – таких, как титан. Детали могут иметь весьма сложную геометрическую форму, делающую изготовление цельных образцов с помощью литья или механической обработки невозможным или весьма дорогостоящим. Поэтому детали приходится изготовлять из нескольких составных частей, подлежащих затем сварке в единое целое. Именно сварочные швы оказываются слабым звеном космических аппаратов и самолетов за счет нарушения однородности материала или окисления при сварке.
Аддитивное производство не ограничено геометрической сложностью изготовляемых деталей – практически любая форма может быть выполнена без последующей сборки или сварки. Единственное ограничение - размер рабочей камеры печатающего устройства. Конструктивных ограничений по размеру не существует. Вопрос лишь в стоимости. Между тем, китайская компания Nanfang Ventilator Co., Ltd уже берется за создание промышленных 3D принтеров аддитивного типа для производства крупногабаритных металлических деталей – до шести метров в длину и весом до 300 тонн.
Сейчас NASA исследует возможности перенесения трехмерной печати в космос, чтобы изготавливать необходимые для ремонта детали и устройства непосредственно на космическом корабле.
В трехмерную печать идут промышленные гиганты: Boeing, General Electric, Lockheed Martin, Mitsubishi, General Motors.
Единственным сдерживающим фактором является себестоимость. Стоимость 3D принтеров, конечно, снизится с повышением спроса. Однако сам спрос зависит от высокой цены расходных материалов.
Печать электронных и электромеханических компонентов фактически ограничит возможности владельцев трехмерных принтеров только лишь их собственной фантазией, как метко замечает Сингер.
Трехмерная печать с комбинированным использованием пластиков и металлов может теоретически позволить создание почти любого устройства и и реально поставить крест на авторских правах.
Конечно же, такие времена пока еще не близки, и не только потому, что сама технология 3D-принтеров, печатающих металлом, еще слаборазвита, но и ввиду недоступности определенных материалов: вряд ли кто сможет достать порошкообразный германий для трансивера мобильного телефона.
Методы трехмерной печати исследуются и в России, и что особенно радостно для меня – в моей alma mater - Самарском государственном аэрокосмическом университете им. академика С.П. Королева.
Здесь разрабатывают первый российский 3D-принтер, работающий с металлом. Ученые СГАУ усовершенствуют лазерную методику, что позволит создавать «крупные элементы и узлы авиационных двигателей, которые изготавливаются из жаростойких и тугоплавких металлов. Разработчики надеются, что в будущем технология 3D-печати сможет вытеснить более дорогостоящие – штамповку деталей и литье.
Принцип работы российского устройства не похож на привычные способы трехмерной печати. Его особенность – более совершенная система подачи материала.
«Зарубежные аналоги, работающие по технологии селективного лазерного плавления, выполняют задачу сравнительно долго, выпекая модель последовательно – слой за слоем. В российской разработке лазерное излучение подводится в точку подачи спекаемого порошка. За счет этого производительность принтера повышается в несколько раз. Это особенно актуально для производства крупногабаритных деталей сложной формы», - рассказывает пресс-служба СГАУ.
В университете разрабатывают сопло – кран, подающий порошок на печать. Вариант, придуманный учеными, позволяет сразу запекать порошок в месте подачи на контур детали. В этом поможет специальная оптическая система, контролирующая расчет порошка и последующее его распределение. Макет технологической головки сопла и элемент наплавления изготовят до конца этого года.
Первыми воспользоваться возможностями российского 3D-принтера смогут на самарском предприятии, выпускающем авиационные и космические двигатели «Кузнецов» – образец детали после испытаний установят на действующий двигатель».
Самарские ученые полагают, что разрабатываемая ими технология имеет преимущества перед аддитивным производством, так как не нуждается в громоздкой и тяжелой радиационной защите.
Возвращаясь к статье Питера Сингера, заметим, что очерченные им новые горизонты индустриального развития органично вписаны в грандиозную программу перевода американской индустрии на шестой технологический уклад.
Хочется верить, что среди первопроходцев новой технологической и индустриальной эры окажутся и российские ученые и промышленники.
Автор: Владимир Прохватилов, Президент Фонда реальной политики (Realpolitik), эксперт Академии военных наук
Больше новостей и ближе к сути? Заходите на ленту в Телеграм!
Добавляйте CСб в свои источники ЯНДЕКС.НОВОСТИ.
//Партнер Гнездо.ру
Картина дня
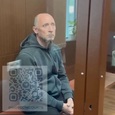
Новости с фронтов борьбы с коррупцией: арест вице-губернатора, задержание мэра, приговор трем генералам
Банки и Дума сильно разошлись по поводу ограничения на допустимое число банковских карт у россиян

К госмессенджеру Max хотят привязать все крупные сервисы

SpaceX успешно запустила Starship после нескольких неудачных пусков

СК возбудил дело в связи с нападением иностранного гражданина на полицейских в Москве около ГБУ "Жилищник"

Hola!: Анна Курникова ждет четвертого ребенка

Суд не стал разводить Романа и Елену Товстиков и дал им время на примирение

//Новости giraff.io
Наши публикации

Гендиректор РКК "Энергия" заявил, что предприятие на грани разорения и вытащить его – "задача из области чуда"
"Ъ": полномочия Бастрыкина на посту председателя СКР продлены, полпредом в этом году он не станет

После резонансной трагедии на Пике коммунизма в Думе предложили запретить восхождения без гидов

Хрен да каша пища наша?

Правительство предложит россиянам добровольно ограничивать себе доступ к опасному контенту в интернете

ЦБ перечислил признаки мошеннических операций при снятии наличных в банкоматах

Чемезов заявил, что в производстве самолетов российские производители движутся гораздо быстрее западных

Слухи, скандалы, сплетни
Hola!: Анна Курникова ждет четвертого ребенка

Анфиса Чехова объявила, что выходит замуж

Суд не стал разводить Романа и Елену Товстиков и дал им время на примирение

Сергей Зверев сообщил о гибели племянника на СВО

Шоубиз
Ксения Бородина вышла замуж за Николая Сердюкова

Виктория Боня о своем восхождении на Эверест: "Удивило молчание коллег по шоу-бизнесу"

Наука
SpaceX успешно запустила Starship после нескольких неудачных пусков

Роскосмос сообщил об устранении утечки воздуха на модуле "Звезда" МКС, о которой известно с 2019 года

«Яндекс» планирует заняться созданием человекоподобных роботов

Корабль Blue Origin с Кэтти Перри и невестой Безоса совершил полет в космос

Хайтек
В сеть утекли 16 млрд паролей от аккаунтов Apple, Google и других сервисов

Разработчики ПО для российской ОС «Аврора» подали заявление о банкротстве

В ФСБ рекомендовали откаться от использования российского браузера "Спутник"

Ъ: В российских кнопочных телефонах обнаружили уязвимость, которая позволяет управлять телефоном посторонним

Туризм
В Европе готовятся запустить новую систему пограничного контроля - контроль за пребыванием ужесточится

Песков: В Кремле не видят новизны в заявлениях Трампа

За поездки за рубеж предложили ввести сбор

Болгария внесла изменения в список документов на получение визы

Спорт
Станислав Черчесов стал главным тренером грозненского «Ахмата»

Дегтяреву неловко называться президентом и он просит себя переименовать

Двукратная олимпийская чемпионка по биатлону Лаура Дальмайер погибла в горах Пакистана

«Оренбург» сыграет вместо исключенного «Торпедо» в новом сезоне РПЛ

МВД назвало размер взятки арбитру за помощь «Торпедо» в решающем матче

«Торпедо» исключили из числа участников РПЛ, но клуб «будет жить»

Вкусный раздел
Юлия Дианова: Не просто завтрак

Дарья Близнюк: «Заготовки от Даши. Вкусно, как ни «крути»!

Анна Аксёнова: Муссовые торты. Легче легкого!

Софи Дюпюи-Голье: Мир хлеба. 100 лучших рецептов домашнего хлеба со всего мира
